
8 Tips To Improve Fine Material Washer Uptime and Sand Production
Fine Material Washers are low horsepower (kW) sand dewatering devices that are used for washing, classifying and dewatering sand in construction aggregate wet washing plants. They are available in single or double screw configurations, with selection being determined by sand solids capacity and water volume flow.
Fine Material Washers are equipped with an Eagle gear reducer, conveyor shaft, wear shoes, washer tub and feed box. Optional equipment includes a discharge chute, washer supports, safety covers and pillow-block rear bearings.
Washing is the primary function of the Fine Material Washer. It is achieved by the continuous rotation of the conveyor shaft and the velocity of the overflowing wastewater. The rotating shaft causes the feed material to roll and tumble, providing particle-on-particle attrition that allows many deleterious coatings to be removed from the sand product and discharged with the wastewater.
The second function of the Fine Material Washer is classification. Classification is achieved by adjusting the volume of water that flows over the back and side weirs of the washer tub. To achieve maximum material retention, the three weirs should be set level to each other to provide a low overflow velocity. A calm pool area is key to efficient classification. This allows the product sized solids to settle out and any fine particles to overflow with the waste.
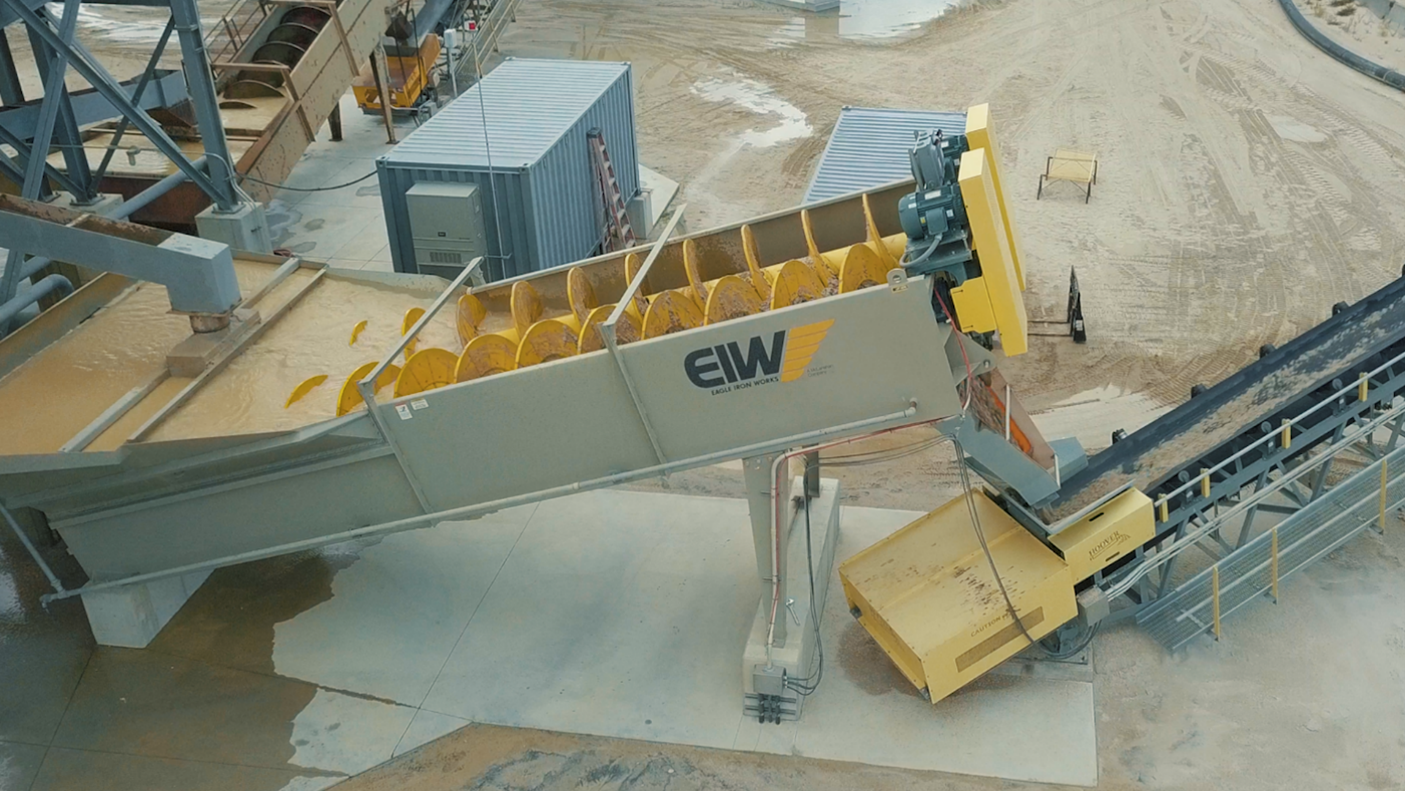
The third function of the Fine Material Washer is dewatering. Dewatering is accomplished by conveying the product from the washer tub up the inclined dry deck area, which allows a lot of the free water to drain from the material. The use of a close-clearance curved plate on one side of the dry deck area and a drainage trough on the other also aids in the dewatering process.
Operational best practices
Fine Material Washers are a tried-and-true method for washing, classifying and dewatering sand. While they have been used in wet processing plants for decades and many aggregate producers are familiar with how they work, here are some operational tips and best practices for helping you get the most out of your Fine Material Washer.
1. Slow the screw speed for finer sand processing
Screw speed is determined by the percent passing 50 mesh. Finer material needs more time to settle out in the washer tub, so slower screw speeds are necessary.
Screw speed can be calculated by dividing 1,500 by the percent passing 50 mesh. For example, if 15% of the material is passing 50 mesh, the screw should be operated at 100% speed for optimum operation. If the sand is slightly finer and contains 20% or 30% passing 50 mesh, the screw should be run slower at 75% and 50% speed, respectively, for optimum operation.
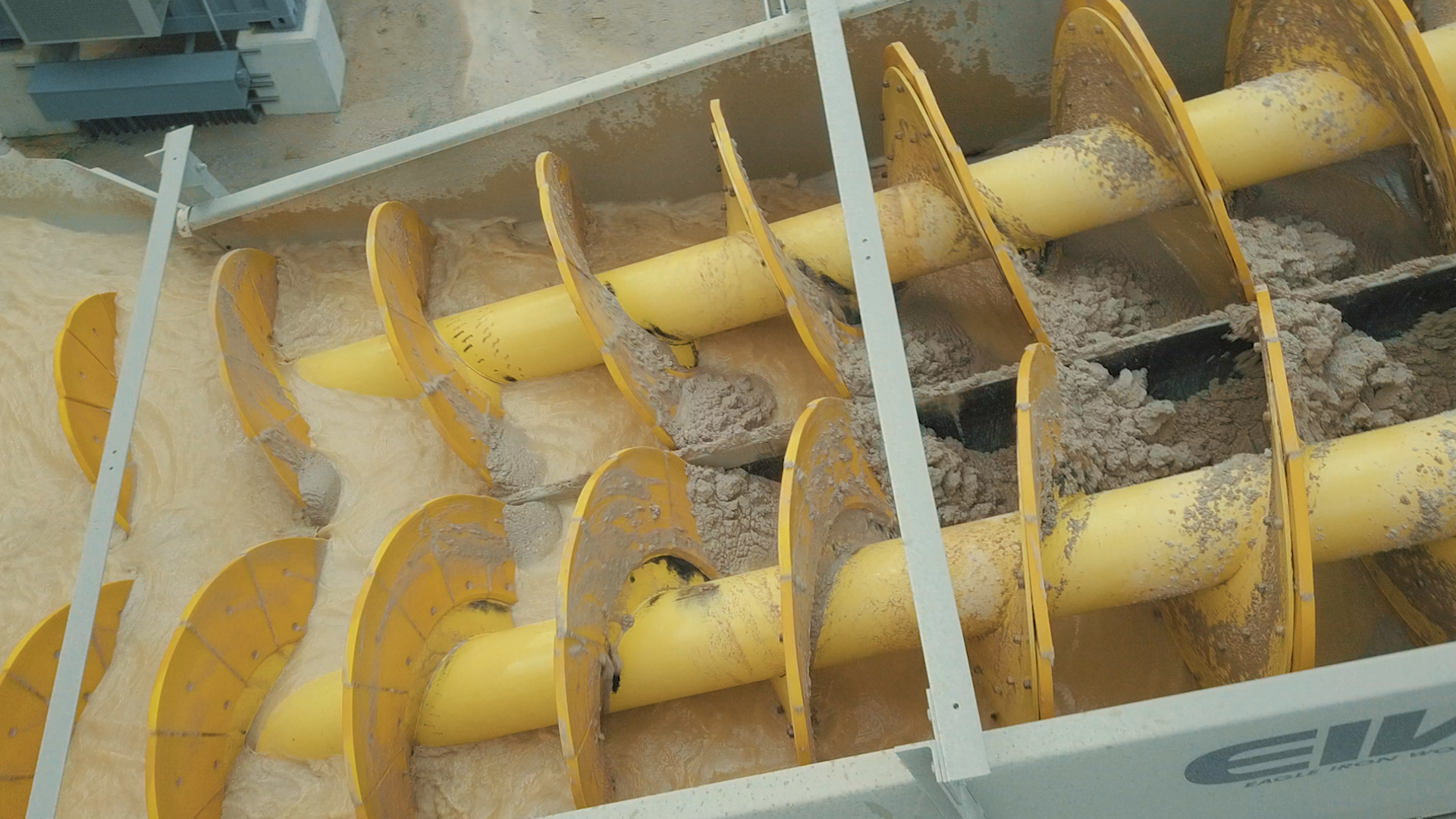
Keep in mind that slower screw speeds result in less capacity and less tons per hour coming off the end of the machine. However, it is important you do not run your screw at higher speeds just to meet capacity, as excessive screw speeds can hurt an operation.
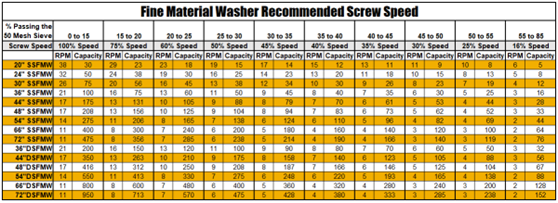
With excessive shaft speed, fine material can build up in the corner of the washer tub. This occurs because the screw is moving too fast for the fine sand to be conveyed toward the discharge. After a few hours of operation at excessive speeds, you will see the resulting tub corner buildup as well as the entire pool area filling with fine sand that eventually overflows product-sized fine sand to waste.
2. Consider adding more processing steps
Additional processing steps are required when a sand feed has a high amount of minus 200 mesh or 0.075mm material. Generally, when you have more than 12-15% of minus 200 mesh material, you should consider a two-step process. A two-step process involves two stages of washing and can be accomplished with two screws or by a Hydrocyclone feeding a screw.
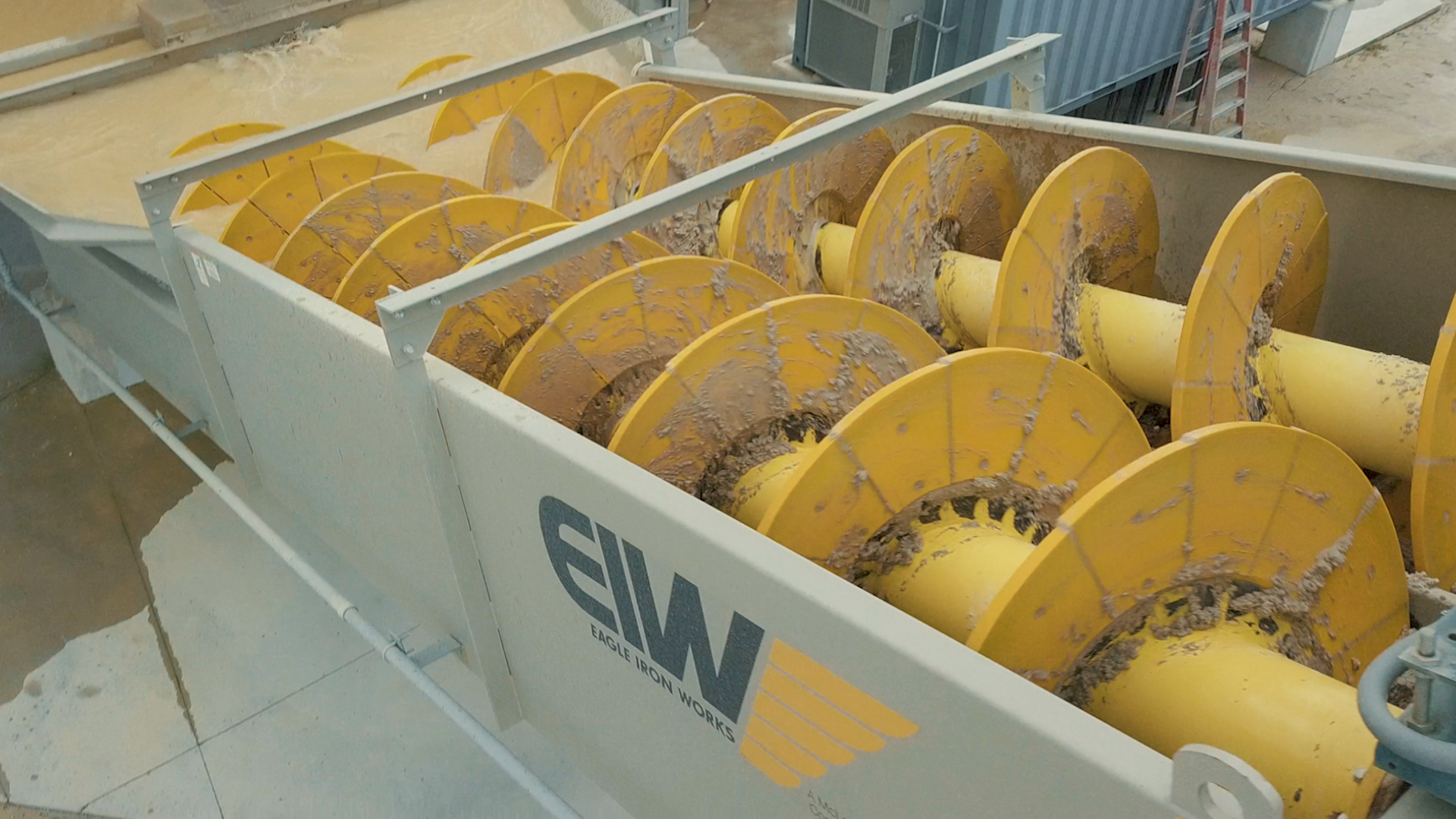
3. Ensure you have enough water
Water is imperative for washing aggregate material, and you need to be sure your equipment is supplied with the appropriate amount of water for optimal operation. As a rule of thumb, Fine Material Washers require 50 gallons of water per minute to remove 1 ton per hour of silt.
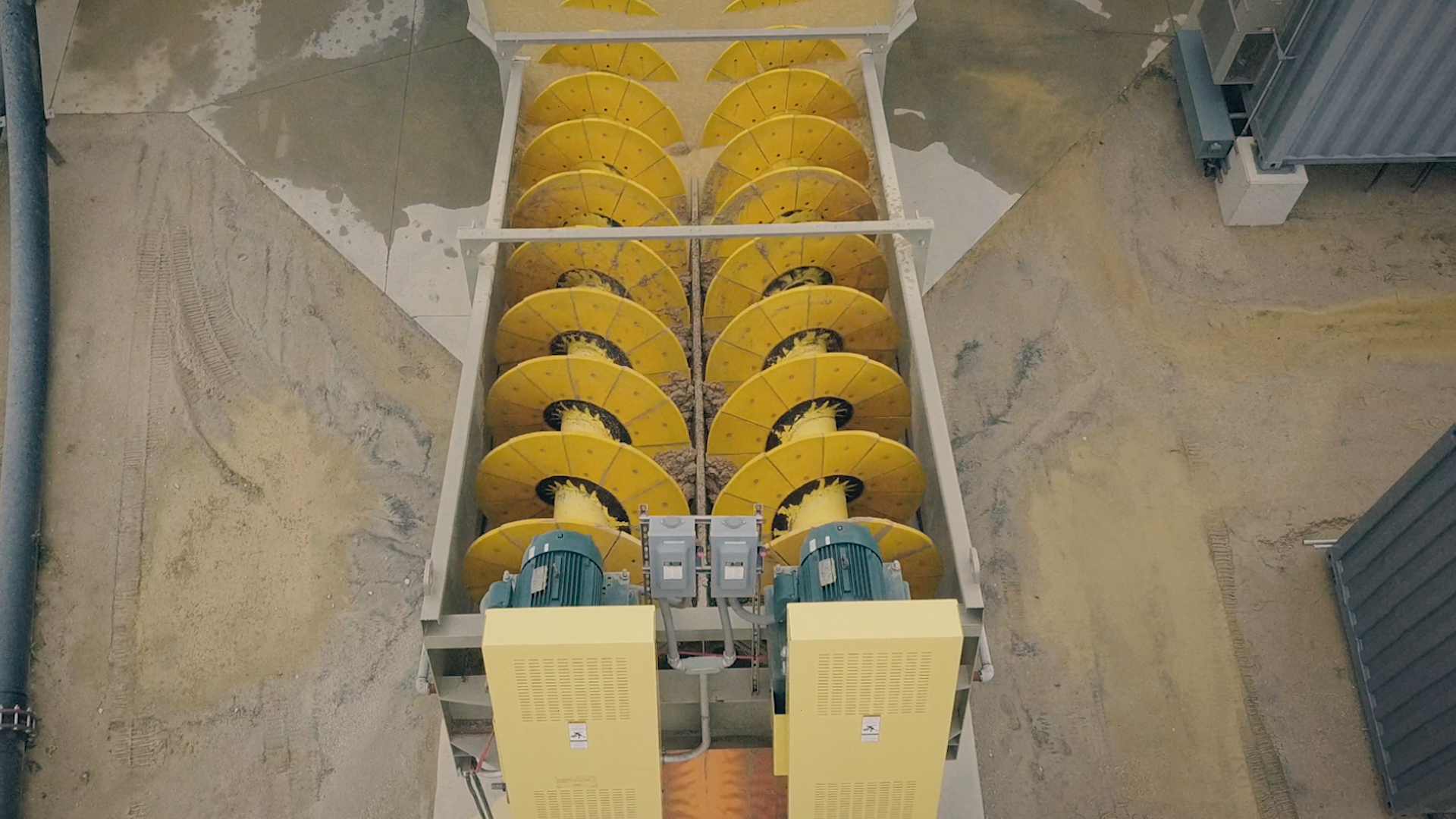
4. Consider adding rising current
Rising current allows for fine-tuning via water injection beneath the pool areas. The addition of clean water improves the classification process. Introducing an upward rising current of water helps to keep the ultra-fines in suspension while the product-sized particles can settle out to be conveyed out of the tub area as product.
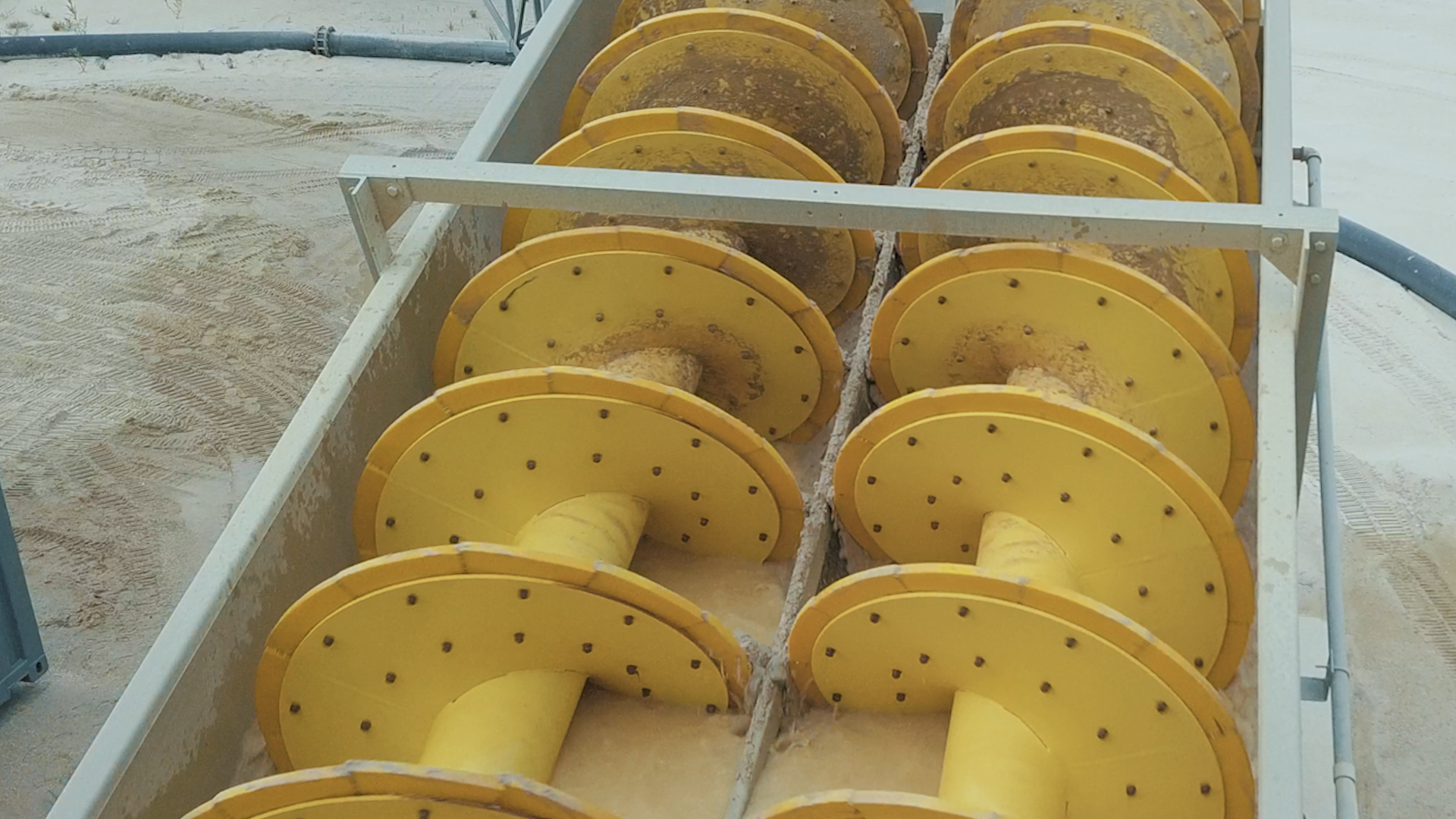
5. Leveling the weirs
Level the weirs on your Fine Material Washer for optimum performance. If you want to get rid of a small amount of excess fines, you can raise the side weirs and lower the back weir. This allows more velocity to overflow the back of the washer to remove excess minus 200 mesh fines.
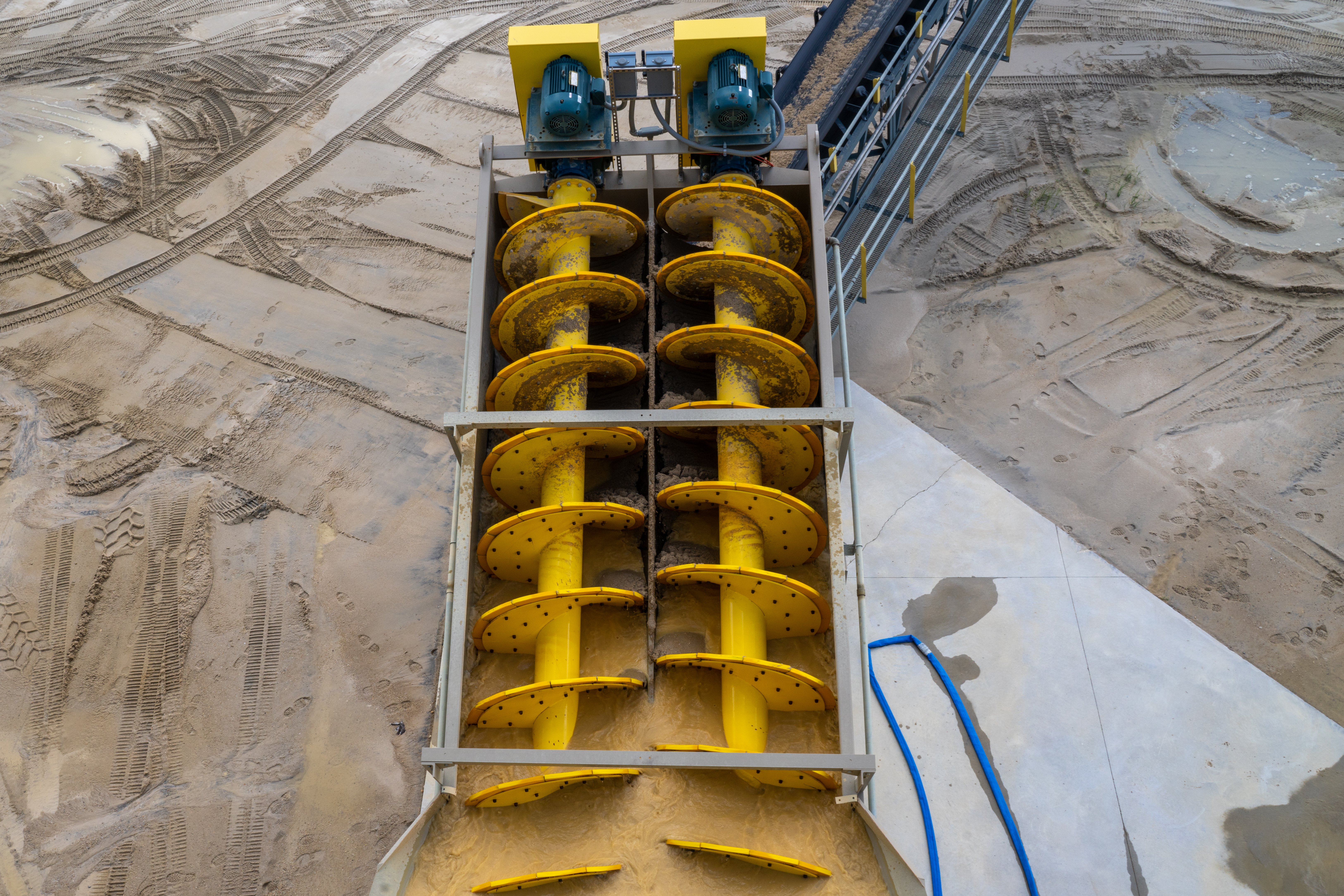
6. Use flush water to decrease buildup
Adding water to the dry deck area of your Fine Material Washer can result in drier sand discharging onto the conveyor and into the product pile. How? The water flushes out any fine sand that has accumulated to allow a clear channel for the water to drain from the sand as it is conveyed up the screw.
7. Ensure you have proper feed entry into a Fine Material Washer
Too much turbulence in the feed area of the washer tub can cause the loss of excess minus 200 mesh fines and potentially some plus 200 mesh fines as well. A feed chute or flume with a velocity break box allows for some turbulence, but not too much.
It is important to have a calm pool area to ensure maximum fines retention so that your sand is making it to the product pile rather than overflowing with the wastewater destined for the settling pond.
8. Make sure your equipment is properly lubricated
Performing routine maintenance and following a regular inspection schedule are important ways to maintain the operating efficiency of your Fine Material Washer. Proper lubrication of bearings is key to ensure optimal performance and unexpected downtime.
Based on a 40-hour-per-week operation, the rear outboard bearing should be lubricated every three months or after 500 operating hours. Keep in mind that over-greasing can damage the seals and plug the drainage port. For any gear box/reducer, refer to the Fine Material Washer’s installation and maintenance manual for gear oil grades and frequency requirements.
Additional equipment used with Fine Material Washers for sand processing
When you have sand equivalency issues, such as too much clay with your feed, and/or too much moisture in your final product, your operation may require additional equipment and processing to remove the undesirable material and/or water.
Some sand deposits will have a slight amount of unsound grains. These unsound grains will break down after several days of exposure to water and air. Even a slight amount of unsound sand becomes dust/excess and can throw your sand out of spec.
Removing this unsound material is often needed to keep your sand product in spec. This can be accomplished with scrubbing equipment, such as a Blade Mill or Attrition Scrubber. Attrition Scrubbers offer more vigorous scrubbing than Blade Mills.
In a typical concrete sand application, Fine Material Washers discharge a product that has 20% moisture content. You can add a skid-mounted Dewatering Screen under the end of your screw to make a drier sand. Generally, using a Dewatering Screen after a sand screw reduces the moisture content by half, resulting in a drip-free product.
CONDOR Fine Material Washers can also be used instead of Classic Fine Material Washers. The two pieces of equipment are similar in size, but a CONDOR machine has a Dodge gear box instead of the classic gear reducer as a more economical and readily available option.
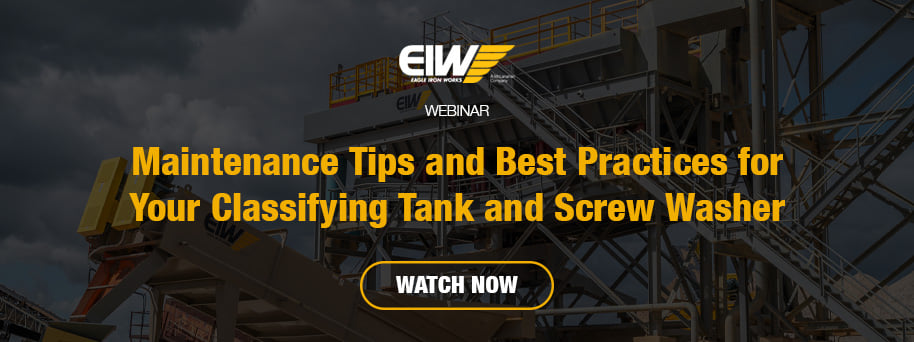
Following these eight operational tips and best practices will help your Fine Material Washer run smoothly with less down time and more uptime for sand production.