
The Basics of Coarse Material Washers
The efficient processing of coarse materials such as gravel and limestone is key to producing clean rock products. Although there are many different types of processing equipment, Coarse Material Washers are a great choice for the washing and scrubbing of aggregates sized larger than 4 mesh. Before integrating Coarse Material Washers into your operation, it is important to know the basics of the equipment.
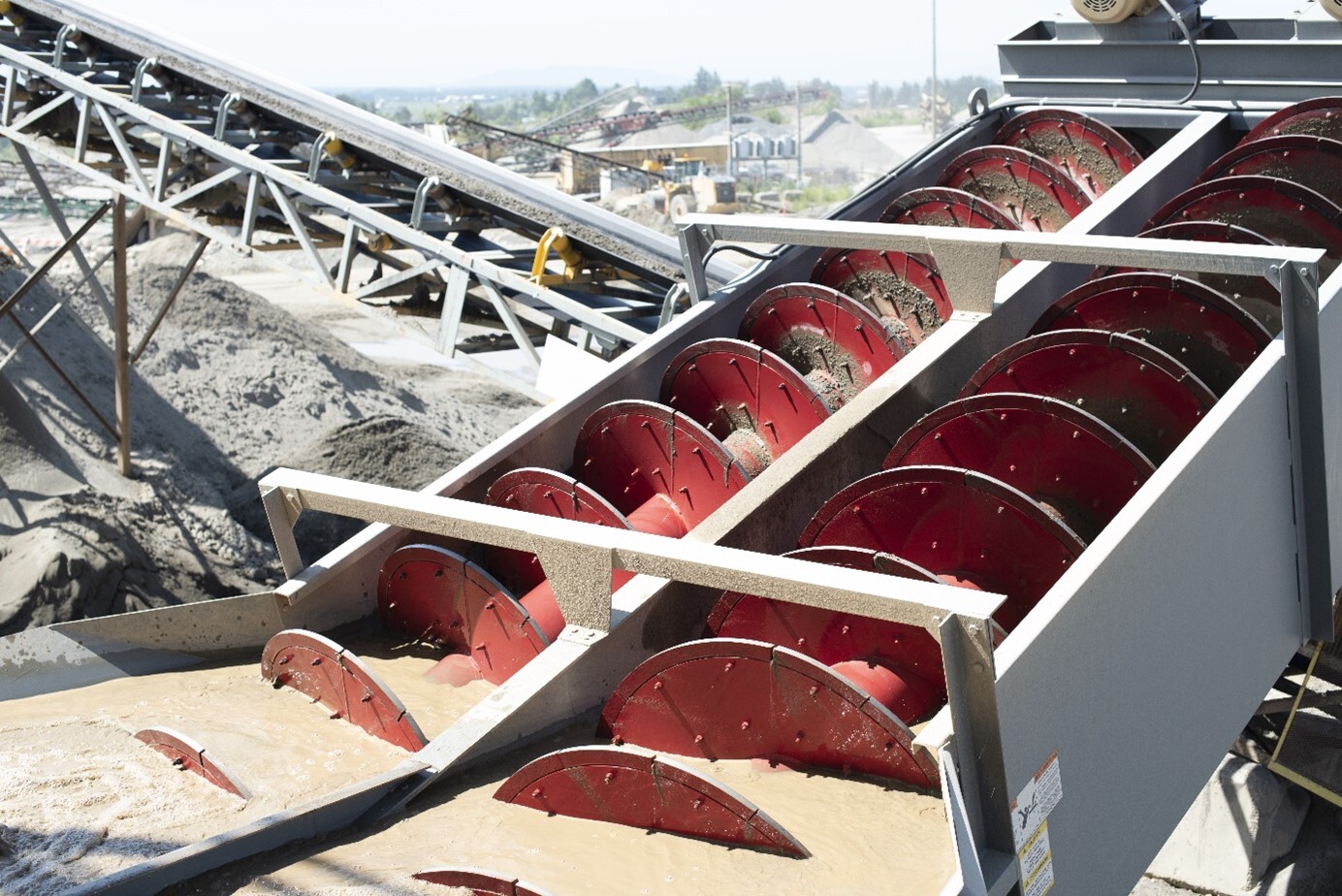
Function of Coarse Material Washers
Coarse Material Washers are heavy-duty machines designed specifically to wash and scrub larger-sized aggregates. The primary function of Coarse Material Washers is to remove undesirable materials such as soluble clays, silts, dirt and contaminants from coarse aggregates. The removal of these unwanted materials is achieved through a combination of agitation, washing and scrubbing with sufficient water.
Coarse Material Washers are specifically designed to handle a range of large-sized aggregates ranging from ¼” to 4” in size, including gravel and crushed stone.
Key Components of Coarse Material Washers
Rotating Spiral Shaft(s): The rotating shaft is the central component of the Coarse Material Washer. It is equipped with paddles in the feed end to provide the scrubbing action, while screw spirals along the remainder of the shaft convey the clean aggregate toward the discharge. The number of paddles on the shaft can be increased to improve scrubbing; however, throughput will be decreased with the addition of extra paddles.
Washer Tub: The tub provides the housing for the aggregates being processed by the Coarse Material Washer. It contains the rotating shaft and is where the aggregates are scrubbed and cleaned.
Rising Current Classifier: The Rising Current Classifier within the tub of the Coarse Material Washer helps to optimize the performance of your machine. An upward rising current addition of water assists in the overflow of unwanted lightweight materials such as twigs, sticks, coals, etc. with the wastewater.
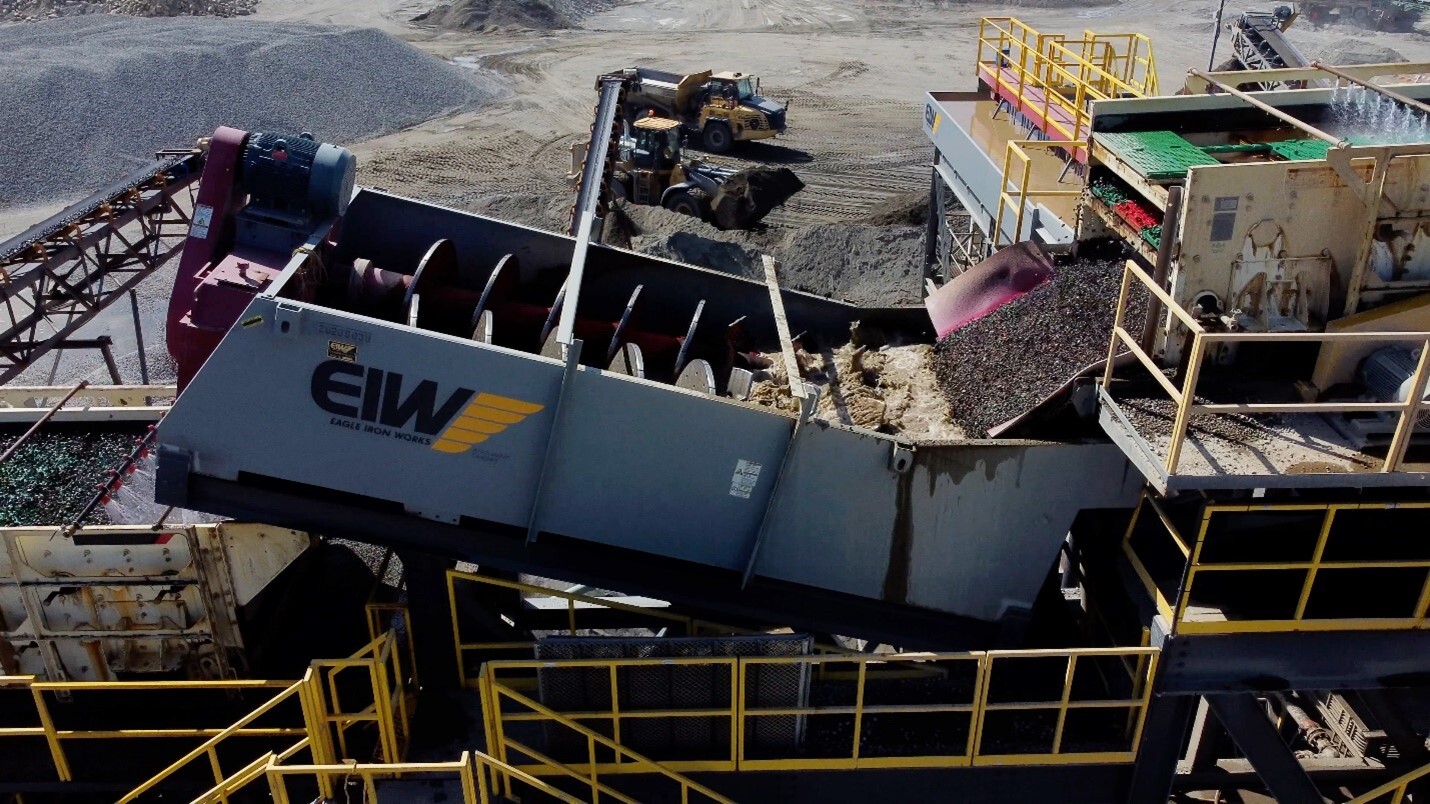
How Coarse Material Washers Work
As material enters the Coarse Material Washer, it encounters the rotating spiral shaft equipped with paddles on the feed end. The rotating motion of the paddles provides particle-on-particle attrition, agitating the material to dislodge and break apart soluble clay and mud contaminants that may be combined with the aggregate.
During this process, the rising current manifold at the feed end of the Coarse Material Washer provides an upward current of water to help remove these unwanted materials. The excess water, along with the washed-out particles, overflow the weir at the back of the Coarse Material Washer, while the clean aggregate is conveyed toward the discharge end.
Adding more paddles to the shaft(s), although reducing capacity, allows material to be retained longer in the tub of the Coarse Material Washer, allowing additional scrubbing to occur.
How to Size a Coarse Material Washer
Sizing a Coarse Material Washer involves careful consideration of several factors. The size of a Coarse Material Washer can typically be determined by the maximum feed size and desired production capacity. Evaluating the characteristics of the feed material, such as its gradation, moisture content and types of contaminants, can also assist in evaluating the necessary size.
Additionally, assessing the required scrubbing intensity and level of cleaning needed for the specific aggregates can help in determining the ideal size and capacity of the Coarse Material Washer for your operation. Considering these factors ensures the Coarse Material Washer’s ability to handle the materials effectively while meeting production requirements.
Most manufacturers will provide a capacity chart. This includes the different sizes of machines offered, along with the maximum feed size, shaft speed, required horsepower and amount of water needed to meet your requirements.
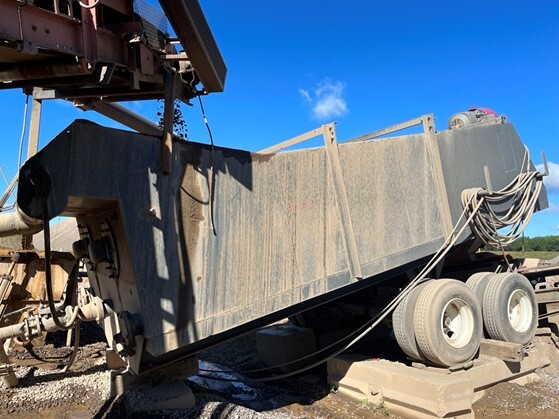
Benefits of Coarse Material Washers
Coarse Material Washers play an important role in ensuring the quality of aggregates for various construction applications. They offer many benefits, such as:
- Ensuring suitability for construction specifications
- Optimizing the aggregate processing workflow
- Providing versatility to your operation
By eliminating contaminants, Coarse Material Washers improve the quality of aggregates, making them suitable for use in concrete, asphalt and other construction materials. The thorough scrubbing achieved by Coarse Material Washers ensures that the resulting product meets strict quality standards ensuring durability in concrete and construction applications.
Coarse Material Washers can help to optimize the aggregate processing workflow, enhancing efficiency and reducing processing time. Because Coarse Material Washers operate on an incline, the dissolved deleterious material is able to overflow the back weir of the machine. With similar pieces of aggregate processing equipment that operate at little to no incline, such as a Blade Mill, the deleterious material cannot overflow and is discharged with the product, requiring further processing.
Coarse Material Washers are also very versatile pieces of equipment for several reasons. To start, they can handle various material types at different feed sizes within the design parameters of the machine and effectively clean these aggregates. Aside from their primary use in aggregate applications, they also play an important role in several other applications, including C&D recycling and concrete reclamation. Lastly, Coarse Material Washers come in various configurations, allowing for customization based on production requirements.
Operational Tips for Coarse Material Washers
- Optimize Water Flow: Ensure a consistent and sufficient water supply during operation. Proper water flow ensures effective washing without causing excessive loss of fines.
- Monitor Speed and Agitation: Adjust the speed of the rotating shaft and the level of agitation to suit the materials being processed. Too much agitation may cause unnecessary wear, while insufficient agitation may result in inadequate cleaning.
- Material Feed Rate: Maintain a consistent feed rate to ensure uniform cleaning and prevent the Coarse Material Washer from being overloaded.
- Adjust for Additional Paddles: When using additional paddles on your Coarse Material Washer, the slope of the machine should be lowered. The amount of power to the motor should also be increased to aid in conveying material to the discharge end of the machine.
- Regular Inspection: Periodically inspect the paddles, spirals and other critical components for wear and tear. Replace or repair worn parts promptly to avoid operational inefficiencies. Use OEM parts to ensure quality and to prevent voiding any existing warranties.
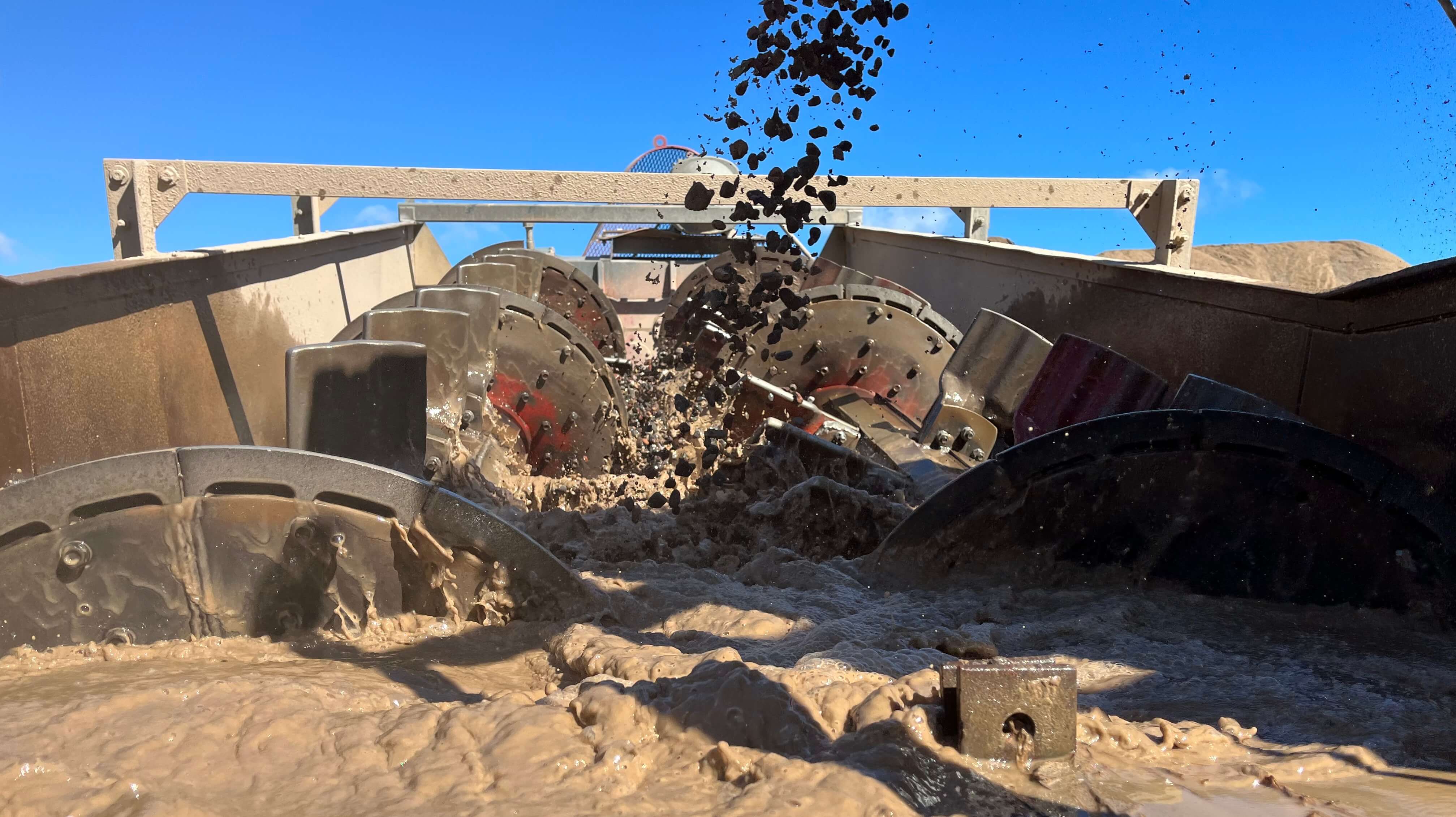
Top Maintenance Activities for Coarse Material Washers
It is important to establish a proper maintenance schedule to keep your Coarse Material Washer operating effectively. Regular maintenance not only ensures the longevity of the equipment but also contributes significantly to its operational efficiency and the quality of processed aggregates. Minimum maintenance activities are usually outlined in the equipment manual.
Paddle or Spiral Maintenance: Regularly inspect and replace worn or damaged paddles or spirals to ensure optimal agitation and cleaning efficiency.
- Bearing and Gearbox Checks: Check bearings and gearbox components for proper lubrication and signs of wear. Lubricate greased bearings and change gear reducer oil according to the maintenance manual.
- Bolt and Fastener Inspection: Check all bolts and fasteners once a week for tightness. Seals should also be inspected for proper performance.
Wear Shoe Condition: Wear shoes should be inspected every three months. These should be replaced before they wear down to the same diameter as the screw flights.
Coarse Material Washers continue to play an important role in the aggregate and minerals processing industry. Understanding their operational principles, the materials they handle, and implementing key operational and maintenance tips are critical for maximizing their effectiveness and ensuring a consistent supply of high-quality aggregates for your production requirements.