
Making Money With Your Classifying Tank
As their name suggests, water scalping-classifying tanks remove excess water and excess sand particles from feed material. They have been used in the aggregates industry to process sand and sand slurries for more than 80 years. Water scalping-classifying tanks are most often used before a fine material dewatering screw washer or a dewatering screen in various plant configurations. They were first used in applications where a fine material screw washer was not able to handle a high water volume or to meet required construction sand specifications.
Water scalping-classifying tanks serve three main purposes in a sand processing application. They remove – or scalp – large volumes of water from the feed material to make further processing easier. They separate sand particles according to their size by employing the principle of hydraulic classification, which allows heavier and coarser aggregate to settle out near the feed end of the tank, followed by the smaller sand particles as they make their way through the tank. Lighter-weight particles like silt are removed with the excess water over the overflow weirs.
The third function of water scalping-classifying tanks is fines retention. This is where classifying tanks outshine fine material screw washers in terms of retaining fine mesh particles. Water scalping-classifying tanks are built with a longer vessel to give the small aggregate particles time to settle. The multiple discharge valves at each station make it easy to produce secondary and tertiary products like asphalt sand, golf sand, masonry/mortar sand, as well as other specialty sands.
Using a water scalping-classifying tank, producers can make multiple products from one feed.
Make Money by Reducing Amount of Non-Spec Sand
Water scalping-classifying tanks re-blend only the desired sand fractions in order to make a primary sand product that meets many construction grade sand specifications. It does this by removing the excess sand at each station. Most applications use classifying tanks to make a primary controlled product using as much of the feed material as possible, while remaining in-spec. The sand particles that are diverted away from the primary product are most often used to make a secondary product. Sometimes, excess particles will be diverted away from the secondary product as well. These non-spec sand particles make up the residual product, sometimes referred to as fill sand.
You can make money with your water scalping-classifying tank by maximizing the amount of in-spec product you make from a single deposit and reducing the amount of fill sand that goes into a lower value product.
You can turn some waste material into a saleable product by efficiently operating your water scalping-classifying tank. Even saving one percent more of the material from going into the waste pile or settling pond by turning it into a saleable product can add up in the long term.
Let’s say your plant produces 500,000 tons of sand per year. If you can save just one percent of material from going to the settling pond, you’ve just produced an extra 5,000 tons of saleable sand product. If sand sells for $8 a ton, then the one percent of sand you saved from going into the settling pond just made you an extra $40,000.
How to Reduce Amount of Non-Spec Sand
To maximize the amount of material used in the final product and reduce the amount of non-spec material headed for the settling pond, you should first understand how water scalping-classifying tanks work. Knowledge of the process can aid in configuring the controls used for product classification. Water scalping-classifying tanks with programmable logic controls (PLCs), like Eagle Iron Works' MarkVI®, will continually optimize the water scalping-classifying tank’s settings to maximize the material to the main product.
Water scalping-classifying tanks work to separate particles according to their size from the moment the sand and water slurry enters the vessel. An elevated lip in the feed box directs the sand slurry past the first two stations.
As the slurry moves along the tank, the sand particles settle out at different stations according to their size and weight, getting progressively finer as they make their way down the tank. Coarser, heavier products settle out near the feed end of the tank, while lightweight, deleterious materials are discharged over the weirs with the scalped water.
After enough material has collected in each station, valves release the precise percentage of material to the appropriate chute of the collecting-blending flume, where the sand is then re-blended to meet product specifications. Each station can have up to four discharge valves, which equates to three controlled products and one residual product. Three discharge valves mean two controlled products and one residual product.
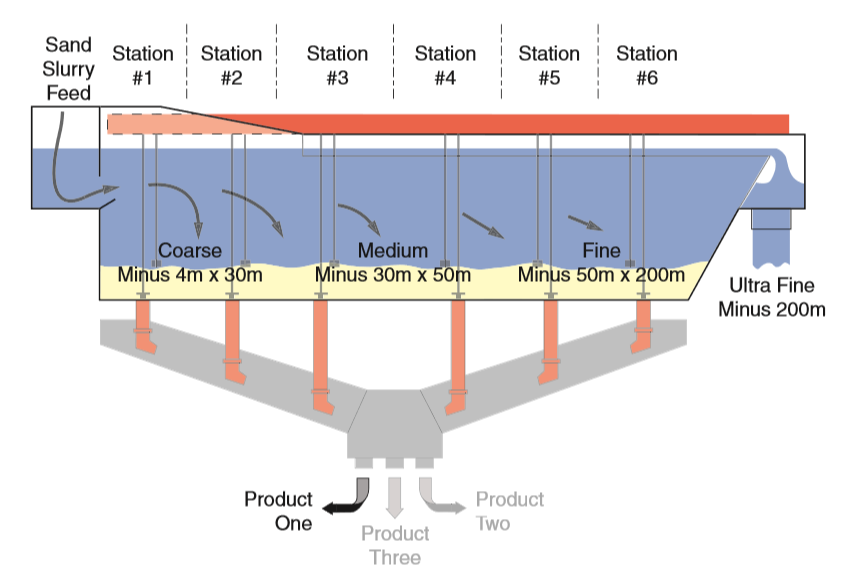
The sand slurry enters the water scalping-classifying tank through the feed box, where an elevating lip gives the slurry an upward kick to keep the medium and fine sands out of the first two stations. As the slurry moves down the tank, the particles settle out at different stations according to their size and weight. Silt and other lightweight deleterious materials are discharged with the scalped water over the weirs. Valves at each station release the material to their designated section of the collecting flume for proper blending.
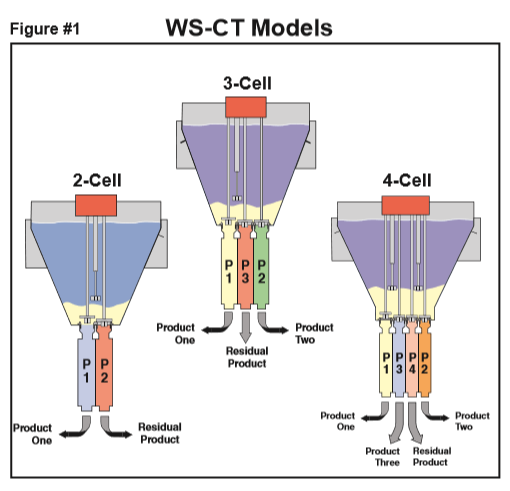
Cross section of water scalping-classifying tank models in 2-cell, 3-cell and 4-cell designs. Water scalping-classifying tanks with two cells create one controlled product and one residual product. Tanks with three cells create two controlled products and one residual product. Tanks with four cells create three controlled products and one residual product.
The percentage of material discharged to each product is controlled at each station. You can choose between 0 and 100% of the particles to be re-blended into the desired products. For example, you can specify 70% of the material in Station #1 to go into Product One and 30% of the material to go into Product Two. If your classifying tank is a 3-cell design and you only want 60% of the material in Station #1 to go into Product One and 30% to go into Product Two, the remaining 10% will be discharged as a non-spec material.
Reducing the amount of non-spec material is as simple as configuring the controls to get the most saleable product out of your feed material while still maintaining product specifications.
Configuring the Controls
Eagle Iron Works Water Scalping-Classifying Tanks come equipped with your choice of re-blending controls: the Digital DIALSPLIT or the Mark VI®. The Digital DIALSPLIT is simple to understand and easy to operate. It allows the operator to control the percentage of material going into each product at each station to ensure product specifications are met.
Eagle’s Mark VI® Control System can run both single and dual tanks with up to 11 stations and two metering bins, and they can produce up to five products with different specifications simultaneously. It offers real time results, as well as predicts tonnages.
With the Digital DIALSPLIT, the operator determines what percentage is required at each station in order to meet the specifications of the final product. The DIALSPLIT percentage settings need to be re-evaluated whenever the feed or the water changes.
The DIALSPLIT control percentage settings can be easily maintained via a cell sample chart of the tank stations.
Before making adjustments to your DIALSPLIT control:
- Take a sieve analysis from each station, as well as from the final product pile.
- Determine if there are deficiencies or excesses of any mesh sizes in the final product.
- Determine which stations those deficiencies or excesses are coming from, and increase or decrease the percentage accordingly.
Note: Making only one change at a time reduces confusion and allows you to take note of each change. Wait at least half an hour before making any remaining changes.
The Mark VI® Control System offers the best in sand re-blending systems. The Mark VI® keeps your product in specification, as well as accommodates any changes in the feed – without any without any manual calculations or recording on your part!
Controlling the Amount of Fines Retained
Water Variations
In a properly planned plant, water is not a variable. Water needs to be consistent at all times. A change in the water will require going back to square one in the setup process. Your water requirements are driven by mining practices (dredge), processing needs (screen deck and anything else that requires water for processing) and silt dilution requirements. After your water needs are calculated, the plant is designed with the water volume locked down. A known water fluctuation is a cyclic change in the sand/gravel ratio of the feed. Because a dredge is usually set to maintain constant power, a change in the sand/gravel ratio usually generates a change in the percent solids of the feed. This equates to a change in the water coming from the dredge. This fluctuation is unavoidable and can change the characteristics of the tank.
Aggregate Gradation Variations
The feed aggregate gradation will affect the end result. There will be gradation fluctuation caused by the lay-of-the-land of the mining, as well as the depth of the mining. The gradation fluctuation falls into two categories: natural fluctuation based on how the material lays in the land, and process fluctuation caused by how you mine, process and handle the material. The process fluctuation will be highly cyclic and very repeatable. Natural fluctuation is usually cyclic but on a much longer time base. The Mark VI® control is designed to help predict the fluctuation and maintain stockpile integrity during these fluctuations.
Silt Variations
Silt will cause the greatest fluctuation in your stockpile. Silt is the guiding hand that chooses where the sand particles land. If you hit a silt seam in the pit, the specific gravity of the tank will get heavy and the different particles sizes will change where they land. More sand will go over the weir and the product will get dirty. Usually, silt is best handled by backing off the tonnage so the water can flush the tank. It is good mining practice to move off the product pile while you are dealing with high silt. You do not want to contaminate the product pile!
If you're looking to retain more fine material during production, Eagle Iron Works’ Water Scalping-Classifying Tanks lead the industry in their design. They feature extra-long adjustable weirs that allow the slurry in the tank to slow down as it progresses down the tank, even in out-of-level conditions.
Each station in an Eagle Water Scalping-Classifying Tank boasts heavy-duty hydraulic cylinders for precise valve discharging and long-lasting paddle motors with sealed sensors. The valve and paddle rods are made of thick steel providing long wear life. These individual components make troubleshooting simpler and reduce maintenance costs. The collecting-blending flume design has replaceable liners to resist abrasion.
For more information about maximizing your efficiency with Eagle Iron Works Water Scalping-Classifying Tanks, the Digital DIALSPLIT or the Mark VI®, contact Eagle Iron Works.
Don’t miss a future post about Eagle Iron Works! Subscribe to learn what Eagle Iron Works equipment can do for you!