
5 Benefits of Dewatering Screens for Sand Washing Plants
Dewatering Screens can be used in a variety of applications, including dewatering, desliming, scrubbing, and washing. Eagle Iron Works' Dewatering Screens are specifically designed to provide a final and more complete drying of a partially dewatered product from a sand screw. They are equipped with high-quality wear liners, heavy-duty urethane screen media and are built to handle high G-forces.
Dewatering Screens are composed of a frame that supports urethane panels and two counter-rotating vibratory motors. Material is fed onto the deck of the Dewatering Screen, where the solids are conveyed toward the discharge end of the screen as a result of motion of the vibrating motors. The screen media on the deck then creates a deep bed of sand that retains particles much finer than the screen openings. The motion of the screen causes the water to detach from the sand particles, where it filters through the material bed and passes through openings in the screen media.
Dewatering Screens can be designed to be operated in a horizontal (flat) orientation or on an incline. Dewatering Screens that are installed horizontally allow for the acceptance of a partially dewatered product where most of the moisture has been removed, such as that from a sand screw or bucketwheel. This makes for a higher discharge point from the screen, which allows stacking conveyors to fit under the discharge chute. Dewatering Screens that are installed on an incline can accept a more dilute slurry, such as that from a cyclone.
In addition to providing the highest level of dewatering short of using various filter equipment, Dewatering Screens also provide the following benefits.
1. Drip-free sand
Using an Eagle Dewatering Screen will aid in reducing moisture content of a final product for easier stockpiling and handling or immediate sale. It can lower the moisture content of your material to around 10%, depending on the application. The discharge from the Dewatering Screen is classified as drip-free and can be easily conveyed, placed in a bin or loaded into a truck for easy transportation. A Dewatering Screen is a low-cost solution for feeding dryers, loading conveyors and trucks, or discharging material to other equipment.
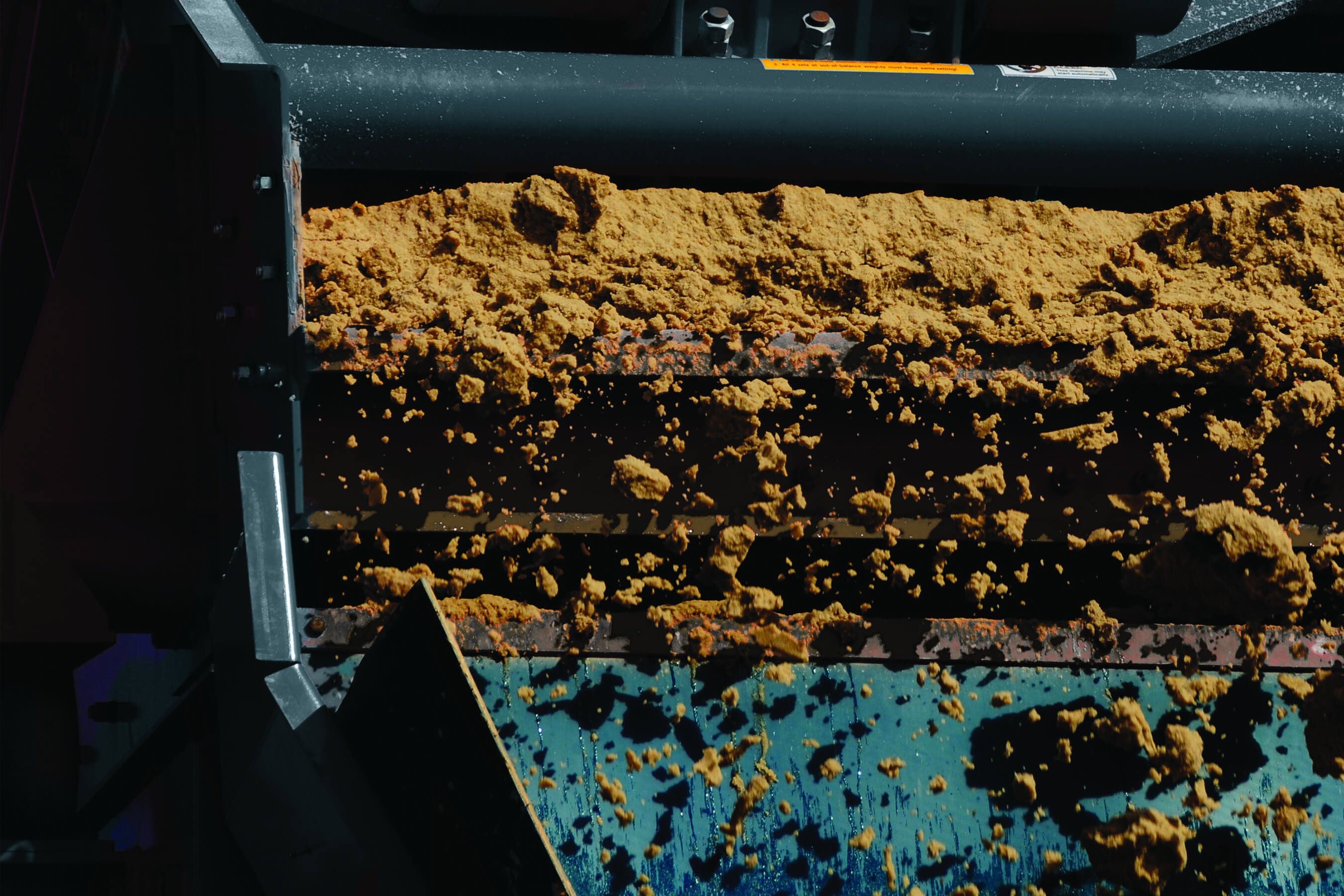
2. Cleaner stockpiles
Stockpiles from Dewatering Screens have less water in them, so they require less drainage consideration. Less water in the stockpiles also means that the product can be moved sooner, which reduces the stockpile footprint as a result. The decreased amount of water draining from the stockpile also minimizes its spread.
Dewatering Screens create taller stockpiles with steeper stacking angles, so more product is housed in a smaller footprint. Dewatering screens also allow for better stockpile management with a shorter inventory cycle.
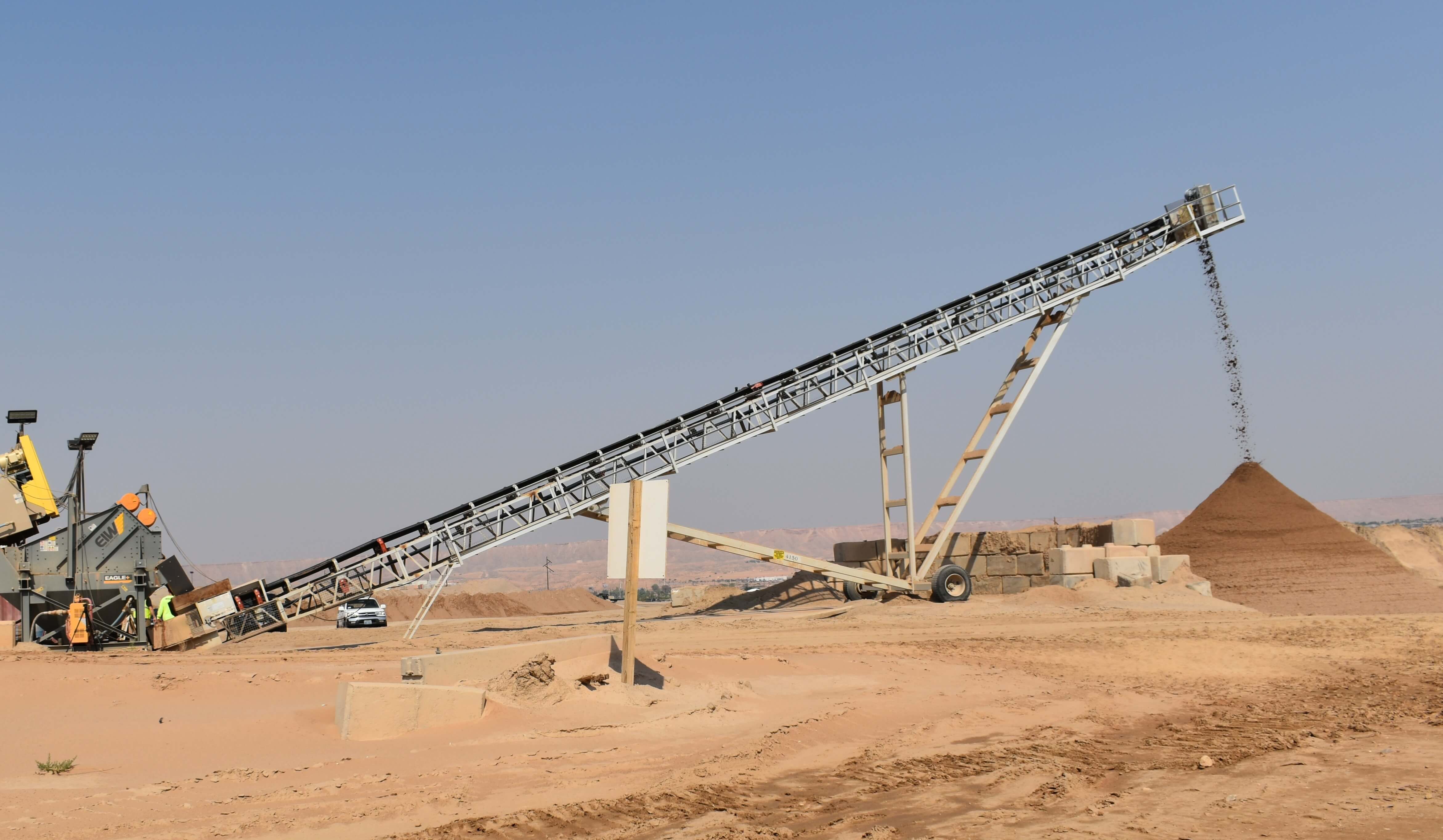
3. Improved housekeeping
Dewatering Screens produce a drip-free product, which allows for a cleaner operating environment with less conveyor spillage to clean up. Because Dewatering Screens remove excess water from the final product, less of a mess is created under the conveyors. With less water in the product, discharge sand doesn’t stick to the conveyor belts as readily, so the returning belt is not spilling sand.
4. Low maintenance
Because dewatered sand doesn’t stick to the conveyor belt as readily, the returning belt does not spill sand underneath the conveyor. This reduces the need for conveyor belt maintenance and limits the use of belt scrapers that remove residual sand stuck to the belt.
In terms of the Dewatering Screen itself, many of the structural components, along with the motor, are designed for heavy-duty applications and require minimal maintenance.
5. Easily integrate with existing equipment
Dewatering Screens are suitable for many different applications, offering a drier product, better control of the process and the ability to capture ultra-fine material. They have a relatively low profile, so a smaller horizontal footprint is required to transfer material.
Dewatering Screens are often placed after a Fine Material Screw Washer to offer further dewatering. The Eagle Dewatering Screen can be added to any brand of screw washer to help minimize moisture content. Fine Material Washers typically discharge material with a moisture content of about 20%. The addition of an Eagle Dewatering Screen will lower that moisture content significantly.
Dewatering Screens can also be used to remove excess water from the underflow of Cyclones that are specifically used for dewatering. This combination of equipment can be used in many applications including, primary washing, size classifications and dewatering. This allows for a higher level of efficiency as well as higher yield with a drier product.
6. Reduce overall water footprint
Water and excess fines can be recycled back into the equipment that is feeding the Dewatering Screen to help with classification. This process minimizes the amount of fresh water needed to produce the material and reduces your overall water footprint as a result.
Dewatering Screens are a key addition to applications that require a drip-free final product because the resulting material has a low moisture content and is stackable and conveyable. Eagle Dewatering Screens provide several additional benefits, including cleaner stockpiles and low maintenance.