
11 Maintenance Tips For Your Coarse Material Washer
Coarse Material Washers are designed to remove soluble clays and dust coatings from aggregate (3/8” to 2-1/2”) feeds. Since removing these deleterious materials is important for creating a clean final product, you’ll want to be sure your Coarse Material Washer is always performing at the highest level.
One of the best ways to do this is by performing routinely scheduled maintenance. Below are 11 maintenance tips to keep your Coarse Material Washer running at optimum levels.
1. Check the oil level on a regular basis.
Check the oil level of your Coarse Material Washer when the machine is in operating position but not running. The oil level should be at the pipe plug opening on the front of the gear case. If the oil level is below the pipe plug opening, add enough oil to maintain the operating level. Oil can be added to the reducer through the pipe nipple that is exposed when the breather cap is removed.
Drain the oil and replace it once a year, or after 2,000 hours of operation, whichever comes first. Select a product with a viscosity that suits the ambient operating temperatures for the local climate. Also, be sure to use only one name brand for the entire fill so as not to worry about base stock or additive package compatibility.
Oil capacity varies for each machine size. Here are the oil capacities for each Eagle Coarse Material Washer size:
- 20” and 24” – 3 gallons
- 30” and 36” – 14 gallons
- 44” and 48” – 19 gallons
- 54” – 34 gallons
- 66” and 72” – 70 gallons
2. Check bearings and motors for excessive heat and noise.
Neither the bearings nor the motors should be excessively hot. If you come across an excessively hot bearing, refer to the Bearings section of your operator’s manual. Likewise, if you come across an excessively hot motor, the Motors section of your operator’s manual will offer solutions for correcting the issue.
Bearings and motors should be checked for excessive heat once per shift. Be sure to remove any debris covering the motor and/or any material buildup on the fins.
3. Perform daily, weekly, monthly, quarterly, six-month and yearly inspections.
Certain maintenance tasks, like changing the oil in the drive reducer, don’t need to be performed as often. Scheduling daily, weekly, monthly, quarterly, six-month and yearly inspections allows you to make the most of your time while still maintaining your machine.
With every inspection, you’ll want to perform the preceding inspections as well. For example, when you perform the six-month inspections, be sure to perform the usual daily, weekly, monthly and quarterly inspections at the same time.
4. Inspect the washer tub for debris.
Inspect the washer tub for any extraneous material that may interfere with the Coarse Material Washer’s startup and its subsequent shaft rotation. Remove any material that could cause issues with startup or rotation.
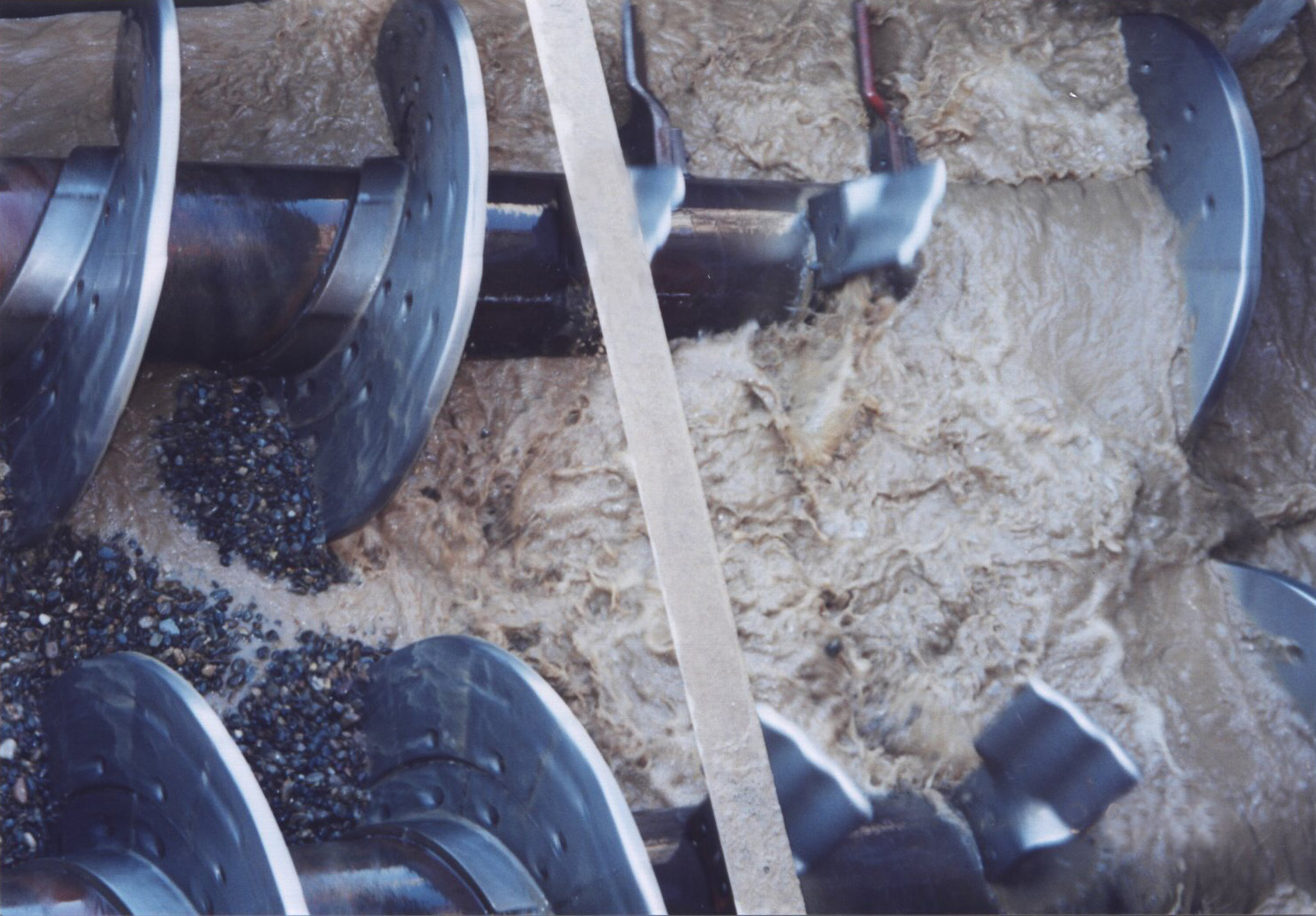
A Coarse Material Washer in action.
5. Inspect V-belts for proper tension and alignment.
Once a week, inspect the V-belts to be sure they are properly aligned and have the appropriate amount of tension. V-belts that are too loose will slip off, while V-belts that are too tight may snap. Check the V-belts for wear or fraying that may indicate improper alignment or tension.
6. Inspect the rubber cover protecting the spider and flanges on the drive member.
Sand or debris must be kept away from the flexible spider that connects the drive member to the shaft. Sand can keep the flexible spider from flexing and promote fatigue failure in both the gear reducer and the shaft. If a rip or hole appears in the rubber cover, replace it!
7. Remove excess grease from outboard bearing vent opening relief slot.
Nine out of 10 failed bearings do so because their outboard bearing vent opening relief slot is plugged with grease. Be sure to keep this relief slot open by removing excess grease that could bridge over and plug the slot.
8. Inspect the wear shoes and paddles for wear.
Once a month, or every 250 hours of operation, inspect the wear shoes and paddles for signs of wear. Worn shoes and paddles won’t clean the material as effectively and may result in loss of production.
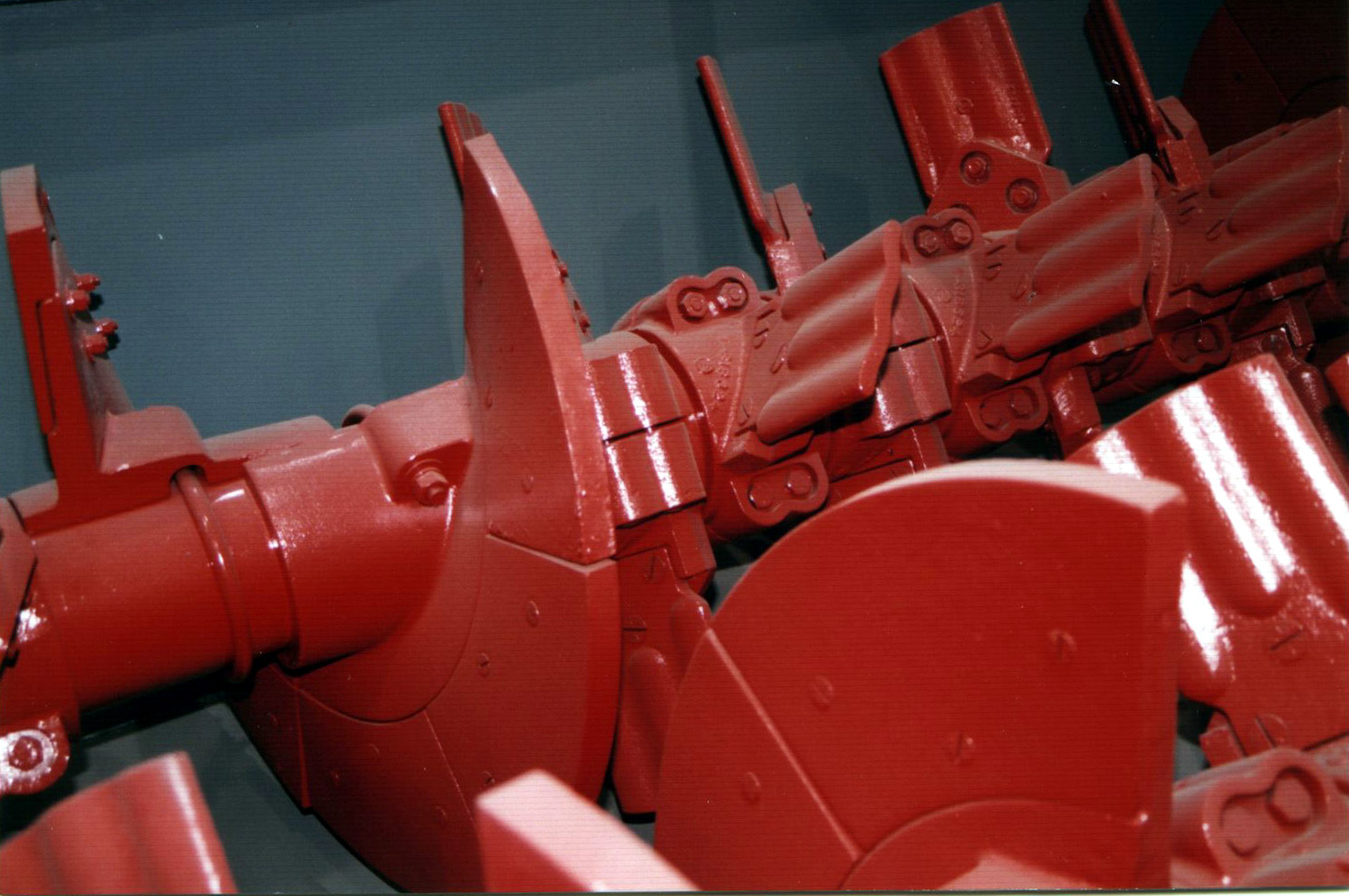
The flights and paddles that make up a Coarse Material Washer shaft.
9. Keep a stock of replacement parts for wear items in stock.
Keeping a stocked inventory of replacement parts readily available helps save on downtime, both unexpected and planned. If you notice during one of your routine maintenance inspections that you need to replace a component, or if an unexpected breakdown does occur, you can take the steps you need to replace the worn component right then and there. You don’t have to lose valuable production time waiting for a replacement part to come to you.
Some common Coarse Material Washer wear parts you want to keep in stock include:
- Bearings
- V-belts
- Wear shoes
- Paddles
10. Make sure that all applicable guards are in place.
This is an important tip. When you are finished performing maintenance, make sure that all applicable guards are in place before resuming normal operation. This should be done after every inspection. No equipment should be run without all of the guards in place!
11. Stick to the maintenance schedule.
What may be the most important maintenance tip is to create a schedule and stick to it. Performing regularly scheduled maintenance checks can save you from unexpected breakdowns, which ultimately lead to costly downtime resulting from lost production. If you don’t have the replacement part you need readily in stock, you have to wait even longer to resume operation.
Following a routine maintenance schedule also allows you to analyze wear patterns on certain components and plan for their replacement – again, avoiding unexpected breakdowns and the downtime associated with them.
It just takes a short amount of time a day to perform an inspection on your Coarse Material Washer, and doing so will help you better plan for future component replacement and reduce unscheduled downtime. Although you can’t completely avoid unplanned shutdowns, performing regularly scheduled routine maintenance can decrease the likeliness of those unplanned shutdowns occurring.